- Home
- Case Studies
- Gießerei
- Boro Foundry – Superheater Header
Wie 3D-Druckund Sandguss die moderne Ersatzteil produktion beeinflussen
Die britische Gießerei Boro Foundry nutzt 3D gedruckte Sandformen für die Produktion von Ersatzteilen. Für eine historische Dampflokomotive fertigte Boro einen neuen Überhitzer auf Basis der damaligen Konstruktionszeichnung. Durch den Einsatz des 3D-Sanddruck konnte die Gießerei 2/3 der Kosten gegenüber einer konventionellen Fertigung einsparen und die Montagezeit des Formpaketes von über 14 Stunden auf gerade mal 3,5 Stunden reduzieren. Projekte wie dieses zeigen eindrücklich, welche Vorteile die additive Fertigung für den Guss bietet – sowohl wirtschaftlich als auch konstruktiv.
Die Dampfmaschine war der erste große Meilenstein der Industrialisierung. Eine mindestens genauso symbolträchtige Stellung nimmt in diesem Zusammenhang aber auch die Dampflokomotive ein. Gewaltige Maschinen mit denen es erstmals möglich war, Personen und Waren über weite Distanzen ohne Pferde zu transportieren. Heute sind diese einstigen Motoren der Industrialisierung noch immer im Vereinigten Königreich im Einsatz, und zwar sowohl auf den Hauptstrecken des Landes als auch regelmäßig auf privaten historischen Eisenbahnen.
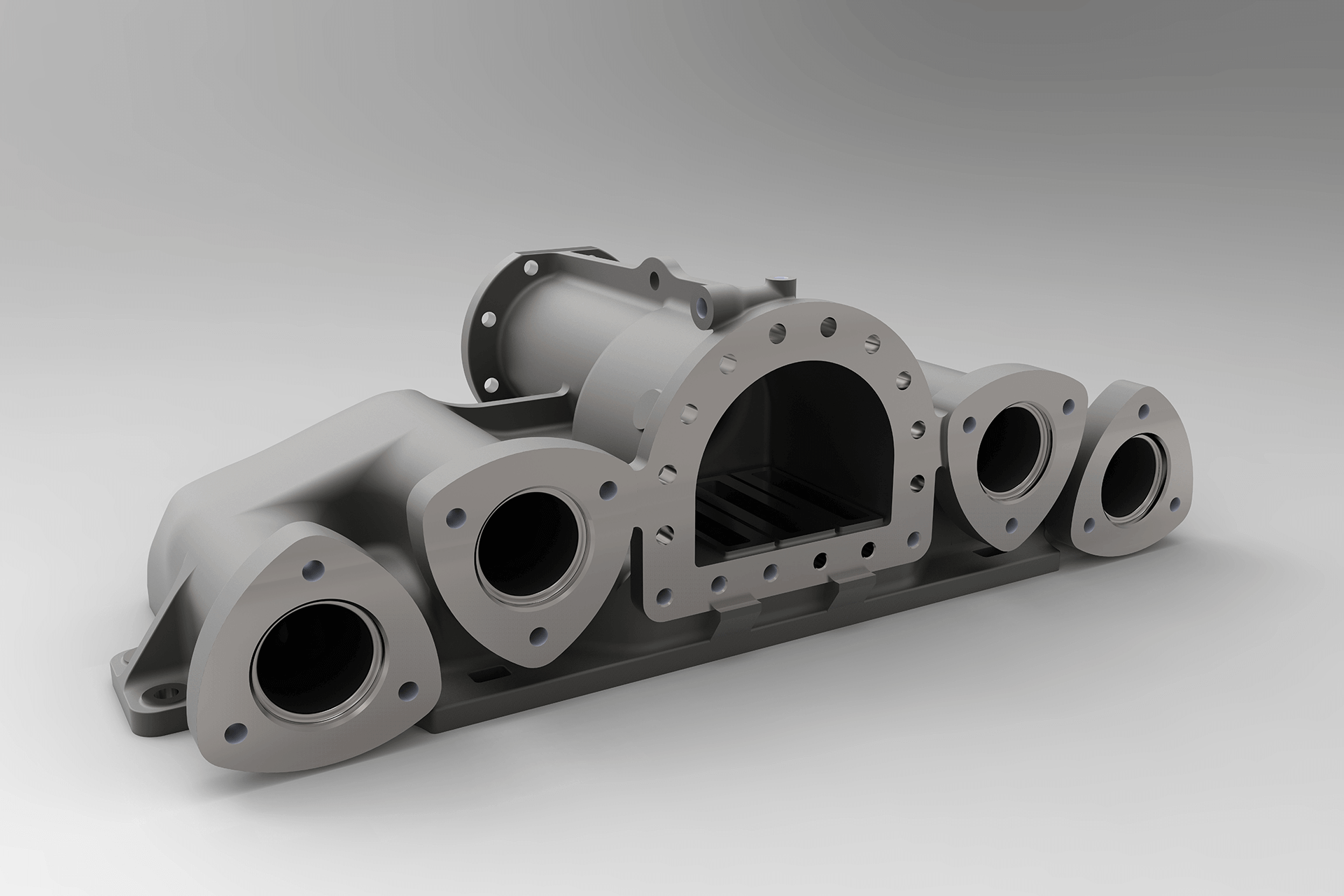
Zu alt, zu teuer, zu ineffizient
Tyseley Locomotive Works aus England ist ein Zentrum, welches sich auf die Restaurierung und Instandhaltung der historischen Dampflokomotiven spezialisiert hat. Anfang 2022 beauftragte Tyseley Locomotive die Boro Foundry Ltd. auf Empfehlung der Universität Warwick mit der Herstellung eines neuen Überhitzermodules für eine ihrer Dampflokomotiven mittels 3D-gedruckter Sandformen. Sam Edwards, Director Sales and Business Development Manager bei Boro Foundry, leitete das Projekt auf Seiten der Gießerei.
Überhitzer spielen für den Betrieb von Dampflokomotiven eine entscheidende Rolle. Sie werden verwendet, um den vom Kessel zu den Zylindern geleiteten Dampf auf Temperaturen weit über der Sättigungstemperatur des Dampfes zu erhitzen
Sam Edwards, Director Sales and Business Development ManagerBoro Foundry
In diesem Fall erzeugt der Kessel Dampf mit einer Temperatur von 202°C, und sein Überhitzer erhöht die Temperatur auf bis zu 340°C, wodurch sich die im Dampf enthaltene Energie (Enthalpie) erhöht, die dann zur Steigerung der in den Zylindern des Motors verrichteten Arbeit genutzt werden kann. Außerdem wird durch die Überhitzung die Kondensation, die bei der Expansion des Dampfes in den Zylindern auftreten kann, auf ein Minimum reduziert, wodurch die Gefahr von Schäden durch übermäßiges Kondensat verringert wird.
Präzision und Qualität standen bei diesem Projekt klar im Fokus, schließlich funktionierte das alte Bauteil mehrere jahrzehntelang einwandfrei, bis es nicht mehr einsatzfähig war“, so Edwards. „Obwohl Überhitzer seit vielen Jahrzehnten in der Lokomotivindustrie verwendet werden, ist das Herstellungsverfahren jedoch veraltet, kostspielig und ineffizient geworden.
Sam Edwards, Director Sales and Business Development ManagerBoro Foundry
3D-Druck stellt die Weichen neu
Das Originalteil enthält nämlich eine Reihe von Löchern (insgesamt 56), durch die während des Betriebes der Dampf geleitet wird und die Herstellung mittels Sandguss stark verkomplizieren. Die größte Herausforderung war der Kern, der in die Form eingesetzt wird, um die Hohlräume bzw. die Löcher ins Gussteil zu integrieren. Ursprünglich wurde der Kern durch Klammern, Bolzen und die Verwendung von Kernstopfen gestützt, damit der Kern während des Gusses statisch an seinem Platz verharrt. Jedoch bestand ein erhebliches Risiko, dass sich der Kern beim Abguss bewegt. Ungleich dicke und dünne Wandabschnitte und eine zusätzliche nachgeschaltete mechanische Bearbeitung wären das Resultat. Eine Inspektion des Originalteils ergab, dass dies die Ursache für die örtliche Ausdünnung gewesen sein könnte, die dazu führte, dass das ursprüngliche Teil aus dem Betrieb genommen wurde.
Angebote für eine traditionell gefertigtes Formpaket, inkl. Modellfertigung hätten bis zu 34.000 Pfund in Anspruch genommen. Darüber hinaus schätzten wir den Zeitaufwand zur Formmontage dieses Formpaketes auf rund 14 Stunden.“ erklärt Edwards, “das alles, gepaart mit dem Risiko, dass das Bauteil am Ende schlecht oder, im schlimmsten Fall, gänzlich unbrauchbar ist, hat uns motiviert nach einer alternativen Fertigungslösung zu suchen. Diese haben wir im 3D-Sanddruck von voxeljet gefunden.
Sam Edwards, Director Sales and Business Development ManagerBoro Foundry
Zukunftsorientiert, kosteneffizient und innovativ
Die ursprüngliche Konstruktionszeichnung war nicht mehr verfügbar und wurde daher von einem Ingenieur von Tyseley neu gezeichnet. Diese Zeichnung wurde anschließend von Stafford Road Design in ein 3D-Modell umgewandelt, das für den 3D-Druck optimiert wurde. Boro Foundry entwickelte zusammen mit dem Ingenieurbüro Cerve Ltd. ein Kernpaket, das aus nur drei Formteilen und einem Kern bestand. Hergestellt wurden die Formen im voxeljet On Demand Printing Zentrum in der Nähe von München.
Als Technologie kommt die Binder Jetting 3D-Drucktechnologie zum Einsatz: Wie die meisten additiven Fertigungsverfahren basiert auch das Binder Jetting auf digitalen CAD-Datensätzen. Diese werden von der Drucksoftware in hauchdünne Schichten „geschnitten“ (engl.: slicing), von denen jede Schicht einen Querschnitt des Objektes darstellt. Dann beginnt der Druckprozess: Ein Beschichter trägt eine mikrometerdünne Schicht des zu verdruckenden Pulvermaterials, in diesem Fall Sand (mittlere Korngröße: 140 µm), auf ein Baufeld auf. Anschließend fährt der Druckkopf über das Feld und bringt selektiv einen Binder in die Bereiche des Baufeldes ein, an denjenigen Stellen, die den Querschnitt des zu druckenden Objektes darstellen. Nun senkt sich das Baufeld um genau eine Schicht, und der Beschichter trägt eine neue Schicht Sand auf, das der Druckkopf wieder selektiv verklebt. Diese Prozessschritte wiederholen sich, bis das Objekt vollständig gedruckt und aus der Box entpackt werden kann.
Ein besonders erfreuliches Ergebnis mit echtem Mehrwert war, dass alle 56 Löcher frei geblieben sind und nachträgliche Bohrungen damit entfielen, was am Ende vom Tag auch wieder enorm Zeit und Geld spart.“ schließt Edwards ab. „Innovation war hier der Schlüssel zum Erfolg. Durch den Einsatz von 3D-Modellierung, Gießsimulation und 3D-Sanddruck konnten die Gesamtqualität, der Zeitaufwand und die Kosten erheblich verbessert werden. Mit der Anwendung dieser neuen Technologien haben wir einen überwältigenden Erfolg erzielt. Dies ebnet den Weg für eine bessere Zukunft bei der Herstellung von Produkten wie diesem Überhitzer und bietet die Perspektive, in Zukunft auch größere und komplexere Gussteile für solche Anwendungen herzustellen
Sam Edwards, Director Sales and Business Development ManagerBoro Foundry
Dank des 3D-Sanddrucks konnte Boro die Montagezeit für die Form auf 3,5 Stunden und die Gesamtkosten auf etwas mehr als ein Drittel der Kosten für den traditionellen Formen- und Modellbau reduzieren.
Anders als beim Originalteil entschloss sich Boro auch dazu, die Form inklusive der 56 Löcher an der Bauteilunterseite zu drucken.
Zwar bestand bei der 3D-gedruckten Form auch das Risiko, dass der Kern aufgrund des Gießdrucks, wegbrechen und aufschwimmen würde, aber indem Boro Aussparungen für Bolzenschraubverbindungen integrierte, konnte der Kern und die Form mithilfe von Bolzen fixiert werden.
Vor dem eigentlichen Guss simulierte Boro den Gießprozess, um ein Angusssystem zu konstruieren, welches den Gießdruckdruck und die damit einhergehende Gefahr zur Kernerosion oder -bewegung reduziert. Darüber hinaus half die Simulation, den Gasstoß während des Gusses vorherzusagen und das Risiko von Gaseinschlüssen zu verringern. Anschließend vergoss Boro die rund 550 kg Eisen bei ca. 1330 °C. Der neue Überhitzer für Tyseley Locomotive Works ist 1300 x 600 x 400 mm groß und wiegt 406 kg.
Weitere Case Studies
Mit 3D-Druck zum Optimierten Elektromotor
Aiona Cast hat ein Patent angemeldet mit dem sich Elektromotoren deutlich optimieren lassen. Einen Prototyp fertigte das Unternehmen mit 3D-Druck an.
Die schnellste Gießerei Skandinaviens
Mit einer neuen VX2000, einem 3D-Sanddrucker für Metallguss stellt Hetitec fertige Gussteile in wenigen Tagen her.
Printed Castings für den Feinguss
Ob Luft- und Raumfahrt, Automobilbau oder Design - die preisgekrönte, amerikanische Feingießerei Aristo Cast setzt beim Feinguss auf 3D-gedruckte Modelle. Erfahren Sie hier warum.
Printed Casting Gehäuse für E-Motorrad
Durch den Einsatz innovativer Technologien wie dem 3D-Druck könnte der Prototyp schon bald in Serie gehen.
3D-Druck für Sandguss in Portugal
CINFU ist ein Ausbildungs- und Innovationszentrum für die Gießereiindustrie mit Sitz in Portugal. Mit einem VX1000 3D-Drucker im Haus gewinnt CINFU erhebliche Vorteile bei der Anpassung an die Gießereiindustrie.
Lanulfi Models optimiert Formenbau mit VX2000
Die Integration der voxeljet VX2000 hat Lanulfis Ansatz im Modell- und Formenbau neu definiert. Sie bietet erhebliche Reduzierungen der Durchlaufzeiten und verbessert die Gestaltungsmöglichkeiten.
PMMA 3D-Druck erobert Nordamerika
Express Prototyping gehört zu den führenden Experten für den 3D-Druck von Feingussmodellen in Nordamerika. Erfahren Sie vom Geschäftsführer Thomas Müller, wie er das Unternehmen gegründet hat und wie er die Zukunft sieht.
Mit 3D-Druck zum Optimierten Elektromotor
Aiona Cast hat ein Patent angemeldet mit dem sich Elektromotoren deutlich optimieren lassen. Einen Prototyp fertigte das Unternehmen mit 3D-Druck an.
Die schnellste Gießerei Skandinaviens
Mit einer neuen VX2000, einem 3D-Sanddrucker für Metallguss stellt Hetitec fertige Gussteile in wenigen Tagen her.
Printed Castings für den Feinguss
Ob Luft- und Raumfahrt, Automobilbau oder Design - die preisgekrönte, amerikanische Feingießerei Aristo Cast setzt beim Feinguss auf 3D-gedruckte Modelle. Erfahren Sie hier warum.
Printed Casting Gehäuse für E-Motorrad
Durch den Einsatz innovativer Technologien wie dem 3D-Druck könnte der Prototyp schon bald in Serie gehen.
3D-Druck für Sandguss in Portugal
CINFU ist ein Ausbildungs- und Innovationszentrum für die Gießereiindustrie mit Sitz in Portugal. Mit einem VX1000 3D-Drucker im Haus gewinnt CINFU erhebliche Vorteile bei der Anpassung an die Gießereiindustrie.
Lanulfi Models optimiert Formenbau mit VX2000
Die Integration der voxeljet VX2000 hat Lanulfis Ansatz im Modell- und Formenbau neu definiert. Sie bietet erhebliche Reduzierungen der Durchlaufzeiten und verbessert die Gestaltungsmöglichkeiten.
PMMA 3D-Druck erobert Nordamerika
Express Prototyping gehört zu den führenden Experten für den 3D-Druck von Feingussmodellen in Nordamerika. Erfahren Sie vom Geschäftsführer Thomas Müller, wie er das Unternehmen gegründet hat und wie er die Zukunft sieht.
Mit 3D-Druck zum Optimierten Elektromotor
Aiona Cast hat ein Patent angemeldet mit dem sich Elektromotoren deutlich optimieren lassen. Einen Prototyp fertigte das Unternehmen mit 3D-Druck an.
Kontakt
Möchten Sie mehr erfahren? Dann fragen Sie uns. Wir helfen Ihnen gerne weiter.
Industrielle 3D-Drucksysteme
Unser Portfolio an industriellen 3D-Druckern reicht vom kompakten System für die Forschung bis zur additiven Serienfertigung.