- Home
- Case Studies
- Gießerei
- 3D-Druck spart Kosten im Sandguss
3D-Druck spart bis zu 75 %an Kosten im Sandguss
Mithilfe des 3D-Drucks lässt sich der Herstellungsprozess von Formen und Kernen drastisch verkürzen. Im konkreten Vergleich zur konventionellen Fertigung, wo die Herstellungskosten bei 3.600 € liegen, lassen sich die gleichen Teile durch den Einsatz von 3D-Druckern auf 900 € reduzieren. Mithilfe des 3D-Drucks lässt sich der Herstellungsprozess von Formen und Kernen drastisch verkürzen. Ganze Arbeitsschritte, wie unter anderem die teuren Werkzeugkosten, können eingespart werden, da für die Herstellung von Sandformen und –kerne lediglich ein CAD-Datensatz notwendig ist.
Durch die werkzeuglose Herstellung von Sandformen und –kernen lassen sich Einzelteile bis Kleinserien wirtschaftlich fertigen. Der Komplexität von Formen und Kernen bei der additiven Fertigung sind dabei – im Gegensatz zur konventionellen Herstellung – nahezu keine Grenzen gesetzt. Denn der Aufwand des 3D-Drucks ist unabhängig von der Komplexität des Bauteils.
Im konkreten Fall zur Herstellung eines Sandkerns für ein Turbinenrad kommen diese Faktoren besonders deutlich zum Tragen. In der konventionellen Herstellung müssen die einzelnen Kernsegmente der Turbinenschaufeln aufwendig zu einem Kern zusammengesetzt werden. Beim 3D-Druckprozess Binder Jetting hingegen wird der gesamte Turbinenkern an einem Stück hergestellt. Der gesamte Herstellungsprozess wird somit deutlich verkürzt. So können bei kleiner Stückzahl bis zu 75% der Kosten eingespart und eine qualitativ gute Reproduzierbarkeit sowie Genauigkeit sichergestellt werden.
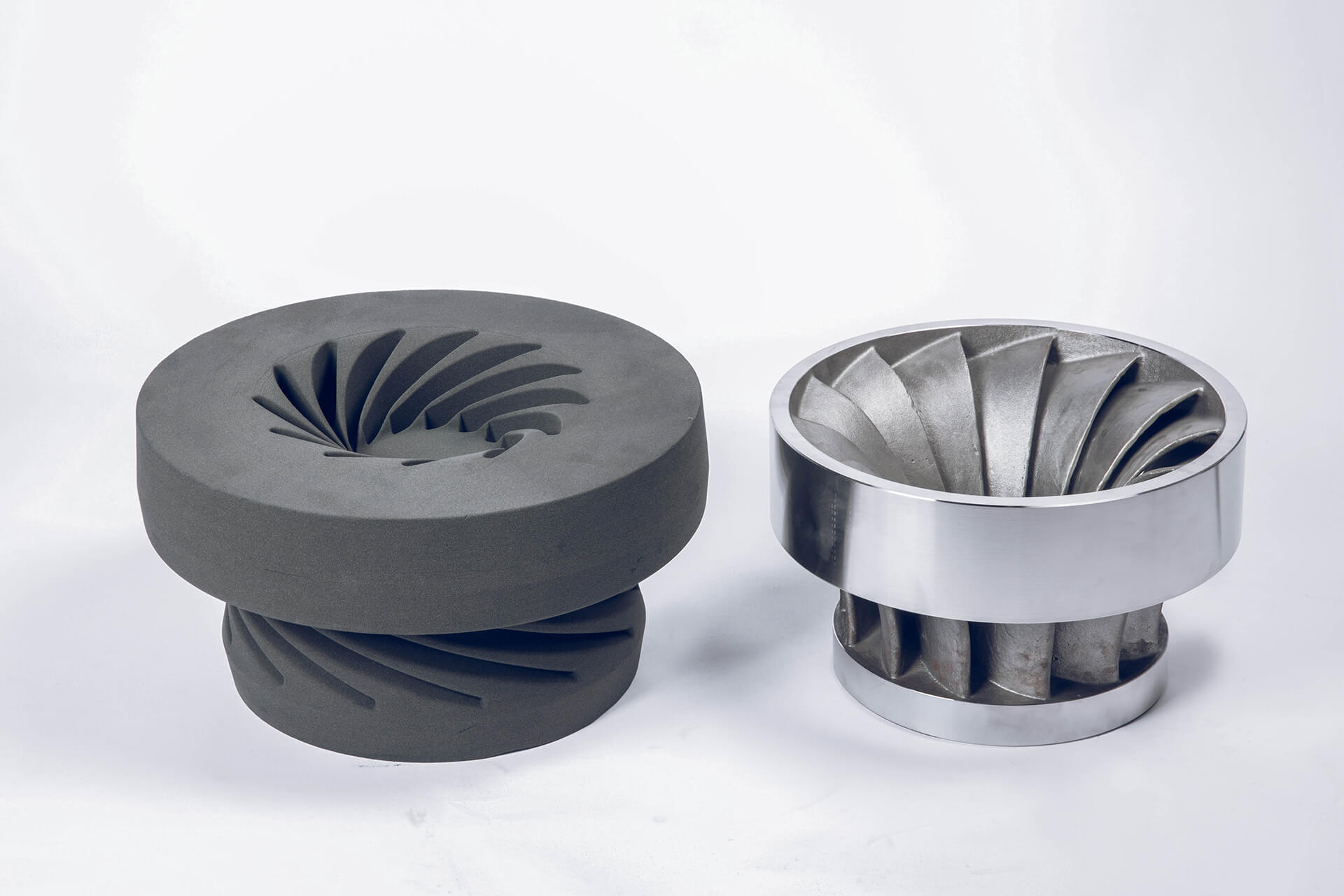
Prototypen bis Kleinserien wirtschaftlich fertigen
Kurze Lieferzeiten und hohe Flexibilität zur Erfüllung unterschiedlichster Anforderungen spielen eine enorm wichtige Rolle. Doch wie lassen sich diese beiden Faktoren sinnvoll und vor allem wirtschaftlich miteinander verknüpfen?
Die Fertigung von 3D gedruckten Sandformen und -kernen ist in nur wenigen Tagen möglich. Im Vergleich zu konventionellen Herstellungsverfahren bedeutet das eine Zeiteinsparung mehrerer Wochen. Zudem wird die Flexibilität in vielerlei Hinsicht erhöht. Zum einen muss nicht auf Hinterschneidungen oder Entformungsschrägen geachtet werden. Zum anderen können notwendige Gusseinrichtungen wie beispielsweise das Angusssystem direkt in den Formkasten konstruiert und mitgedruckt werden. Auch Bauteiländerungen können schnell und einfach umgesetzt werden. Ziel ist es, den Zeit- und Kostenaufwand der Form- und Kernherstellung deutlich zu reduzieren und komplexe Geometrien einfach zu realisieren. Dabei kann eine Hybrid-Bauweise, die 3D-Druck und die konventionelle Herstellung kombiniert, beliebig eingesetzt werden.
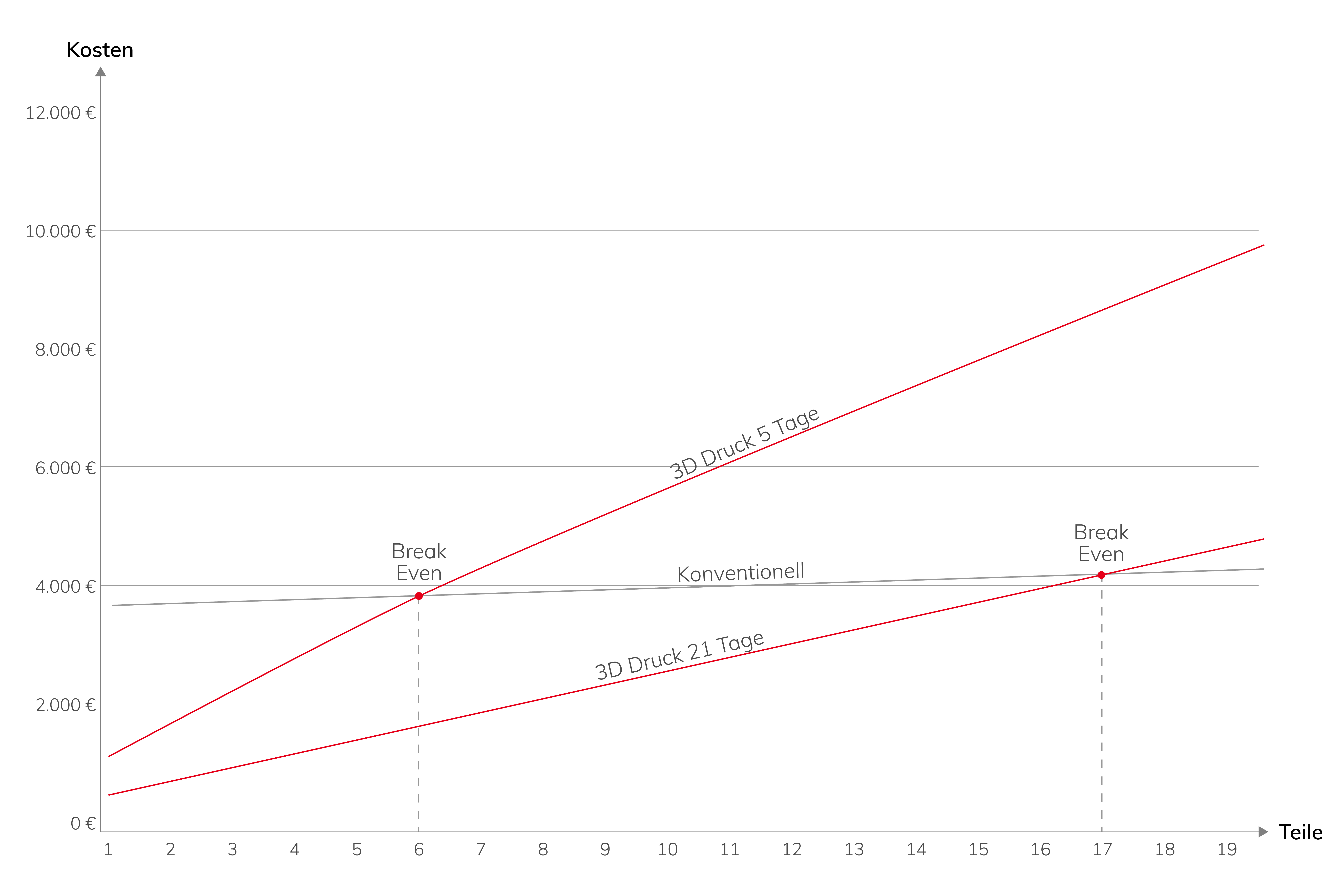
Vom gedruckten Kern zum Fertigen Gussteil
3D-Druck: Sandformen und Kerne beliebiger Komplexität werden über einen Schichtbauprozess hergestellt. Dabei verteilt ein Recoater das Partikelmaterial in einer sehr dünnen Schicht über das gesamte Baufeld. Ein Druckkopf bringt dann Bindemittel selektiv an den Stellen auf, wo später das Bauteil entsteht. Diese beiden Schritte werden so oft wiederholt, bis das gesamte Bauteil realisiert ist. Anschließend wird das Bauteil vom losen Partikelmaterial befreit und nachbearbeitet.
Schlichten: Analog zum klassischen Sandguss wird auch der gedruckte Kern in der Gießerei mit Schlichte versehen, um den hohen thermischen Beanspruchungen standhalten zu können.
Kernmontage: Anschließend wird der 3d gedruckte Sandkern in eine konventionell hergestellte Form eingesetzt. Generell lässt sich eine Hybridbauweise aus gedruckten und konventionell hergestellten Formen beliebig kombinieren.
Abguss: Nun wird das Turbinenrad abgegossen. Mit dem 3D gedruckten Formen und/oder Kernen lassen sich alle gängigen Legierungen gießen. Durch unterschiedliche Sandkörnungen lässt sich die Oberflächengüte beeinflussen.
Entkernen: Wie auch bei der konventionellen Herstellung handelt es sich beim 3D-Druck von Sandformen und Kernen um das Gießen mit verlorener Form.
Nacharbeiten: Nach dem Entformen wird das Bauteil noch nachbearbeitet. Der Aufwand für die Nacharbeit wird durch Anwendung des 3D Druckverfahrens reduziert, da Gussteile bereits über eine höhere Genauigkeit verfügen. Dies ist darauf zurückzuführen, dass selbst komplexe Geometrien mit Hinterschneidungen an einem Stück gedruckt werden können.
Vorteile des 3D-Druck im Überlick
- Zeitersparnis und Kostenersparnis bei kurzen Durchlaufzeiten und werkzeugloser Fertigung.
- Hohe Flexibilität bezüglich Stückzahl und Formdesign.
- Hybridbauweise mittels Kombination mit konventionellen Verfahren.
- Keine Lager- & Instandhaltungskosten für konventionelle Sandformen und Sandkerne.
Weitere Case Studies
Boro Foundry – Superheater Header
Aus der Kombination Sand-3D-Druck konnte die britische Gießerei Boro Foundry ein makelloses Ersatzteil für eine Dampflok herstellen.
Mit 3D-Druck zum Optimierten Elektromotor
Aiona Cast hat ein Patent angemeldet mit dem sich Elektromotoren deutlich optimieren lassen. Einen Prototyp fertigte das Unternehmen mit 3D-Druck an.
Die schnellste Gießerei Skandinaviens
Mit einer neuen VX2000, einem 3D-Sanddrucker für Metallguss stellt Hetitec fertige Gussteile in wenigen Tagen her.
Printed Castings für den Feinguss
Ob Luft- und Raumfahrt, Automobilbau oder Design - die preisgekrönte, amerikanische Feingießerei Aristo Cast setzt beim Feinguss auf 3D-gedruckte Modelle. Erfahren Sie hier warum.
3D-Druck für Sandguss in Portugal
CINFU ist ein Ausbildungs- und Innovationszentrum für die Gießereiindustrie mit Sitz in Portugal. Mit einem VX1000 3D-Drucker im Haus gewinnt CINFU erhebliche Vorteile bei der Anpassung an die Gießereiindustrie.
Lanulfi Models optimiert Formenbau mit VX2000
Die Integration der voxeljet VX2000 hat Lanulfis Ansatz im Modell- und Formenbau neu definiert. Sie bietet erhebliche Reduzierungen der Durchlaufzeiten und verbessert die Gestaltungsmöglichkeiten.
PMMA 3D-Druck erobert Nordamerika
Express Prototyping gehört zu den führenden Experten für den 3D-Druck von Feingussmodellen in Nordamerika. Erfahren Sie vom Geschäftsführer Thomas Müller, wie er das Unternehmen gegründet hat und wie er die Zukunft sieht.
Boro Foundry – Superheater Header
Aus der Kombination Sand-3D-Druck konnte die britische Gießerei Boro Foundry ein makelloses Ersatzteil für eine Dampflok herstellen.
Mit 3D-Druck zum Optimierten Elektromotor
Aiona Cast hat ein Patent angemeldet mit dem sich Elektromotoren deutlich optimieren lassen. Einen Prototyp fertigte das Unternehmen mit 3D-Druck an.
Die schnellste Gießerei Skandinaviens
Mit einer neuen VX2000, einem 3D-Sanddrucker für Metallguss stellt Hetitec fertige Gussteile in wenigen Tagen her.
Printed Castings für den Feinguss
Ob Luft- und Raumfahrt, Automobilbau oder Design - die preisgekrönte, amerikanische Feingießerei Aristo Cast setzt beim Feinguss auf 3D-gedruckte Modelle. Erfahren Sie hier warum.
3D-Druck für Sandguss in Portugal
CINFU ist ein Ausbildungs- und Innovationszentrum für die Gießereiindustrie mit Sitz in Portugal. Mit einem VX1000 3D-Drucker im Haus gewinnt CINFU erhebliche Vorteile bei der Anpassung an die Gießereiindustrie.
Lanulfi Models optimiert Formenbau mit VX2000
Die Integration der voxeljet VX2000 hat Lanulfis Ansatz im Modell- und Formenbau neu definiert. Sie bietet erhebliche Reduzierungen der Durchlaufzeiten und verbessert die Gestaltungsmöglichkeiten.
PMMA 3D-Druck erobert Nordamerika
Express Prototyping gehört zu den führenden Experten für den 3D-Druck von Feingussmodellen in Nordamerika. Erfahren Sie vom Geschäftsführer Thomas Müller, wie er das Unternehmen gegründet hat und wie er die Zukunft sieht.
Boro Foundry – Superheater Header
Aus der Kombination Sand-3D-Druck konnte die britische Gießerei Boro Foundry ein makelloses Ersatzteil für eine Dampflok herstellen.
Kontakt
Möchten Sie mehr erfahren? Dann fragen Sie uns. Wir helfen Ihnen gerne weiter.
Industrielle 3D-Drucksysteme
Unser Portfolio an industriellen 3D-Druckern reicht vom kompakten System für die Forschung bis zur additiven Serienfertigung.