- Home
- Case Studies
- Gießerei
- PMMA 3D-Druck erobert Nordamerika
PMMA 3D-Druck erobert Nordamerika
Geht es um kleine, detail- und maßgenaue Gussteile für den Automobilbau oder die Luft- und Raumfahrt, ist meist vom Feinguss die Rede. Ein jahrhundertealtes mehrschrittiges Gießverfahren, mit dessen Hilfe sich hochkomplexe Bauteile fertigen lassen.
Dank des 3D-Drucks gibt es Möglichkeiten, die Effizienz, Wirtschaftlichkeit und Geschwindigkeit des Feingießens und der Gussteile weiter zu steigern. Mittels PMMA 3D-Druck können so bis zu 75 % an Kosten und Lieferzeiten eingespart werden.
Das in Michigan, USA ansässige Unternehmen Express Prototyping hat sich auf den PMMA-3D-Druck spezialisiert. Vor zehn Jahren gründete der Augsburger Thomas Müller das Unternehmen mit einer mittelgroßen VX500. Heute betreibt er mit drei industriellen VX1000 3D-Druckern eines der größten Dienstleistungszentren für 3D-gedruckte Feingussmodelle in Nordamerika. Wie kam es dazu und welches Potenzial haben Markt und Technologie?
Early Binder Jetting Adapter als One-Man-Show
Im Rahmen seines Maschinenbaustudiums an der Universität Augsburg kam Thomas Müller schon Anfang der Zweitausender mit dem industriellen 3D-Druck in Kontakt. Die additive Prozesstechnologie Binder Jetting war zu dem Zeitpunkt gerade mal ein paar Jahre alt, als Thomas Müller 2001 seine Diplomarbeit bei der damaligen Generis GmbH schrieb. Als Servicetechniker und Wartungsexperte baute er die folgenden Jahre sein Know-how rund um die additive Fertigung für den Metallguss aus. Es folgte ein Jobangebot, für das er 2008 in die USA zog.
Der Industrie und der Technologie blieb er weiter treu und arbeitete Übersee als Produktionsleiter mit dem Sand 3D-Druck. Dort installierte voxeljet auch den ersten PMMA Drucker für die Feingussindustrie in Nordamerika. Eine Innovation, die Thomas von Tag eins an faszinierte. 2012 beschloss er dann, sich vollständig auf dieses Marktsegment zu fokussieren und machte sich selbstständig.
Da der Feingussprozess bereits seit mehreren Tausend Jahren existiert, stellt sich die Frage, wie ein solch etabliertes Verfahren noch Möglichkeiten zur Innovation und Optimierung bietet. Dazu lohnt es sich, den Prozess und die einzelnen Schritte des Feingießens besser zu verstehen.
Er erwarb eine VX500 von voxeljet und installierte diese direkt in einer Feingießerei. Von da an belieferte er sowohl die Gießerei selbst, als auch seine bereits bekannten und vertrauten Kunden aus den unterschiedlichsten Industriezweigen. Sein Angebot: schnelle Prototypen, einfacheres Handling während des Schalungsprozesses und höchste Qualität, selbst bei komplexen Strukturen.
Der wesentliche Zeit- und Kostenpunkt beim Feinguss ist der Modellbau. Die Herstellung solcher der Modelle über Spritzgusswerkzeuge kann mit konventionellen Methoden bis zu 12 Wochen dauern und mehrere Zehntausend Euro kosten. Mit dem 3D-Druck kann ein Modell deutlich günstiger und deutlich schneller, da vollkommen werkzeuglos, hergestellt werden. Sowohl Produktions- und Lieferzeit, als auch die Kosten können durch den Einsatz von 3D-Druck um rund 75 % gesenkt.
Sollen gleich mehrere Designentwürfe oder Varianten gleichzeitig getestet werden, können diese simultan 3D-gedruckt und gegossen werden, anstatt unter hohem Aufwand mehrere Modelle über Werkzeuge herzustellen, die im schlimmsten Fall nie wieder genutzt werden, da das Design verworfen wird. So kann 3D-Druck-gestützter Feinguss insbesondere Produktentwicklungszyklen und Ersatzteilbeschaffungen optimieren und beschleunigen.
Den Großteil seiner Kunden kannte Thomas noch von vorherigen Projekten. Zum Kundenkreis gehörten fast ausschließlich Firmen aus dem Automobil- und Landmaschinenbau und der Luft- und Raumfahrt. Aber auch ein paar exotischere Projekte, wie die Herstellung von Football-Helmvisieren belieferte Express Prototyping bereits. Aufgrund der hervorragenden Ausbrenneigenschaften wuchs die Nachfrage nach 3D-gedruckten PMMA-Modellen so kontinuierlich an, bis die Kapazität der VX500 nicht mehr ausreichte. Die Lösung lag für Thomas auf der Hand. Er tauschte seine VX500 gegen eine leistungsstärkere VX1000. Es folgte eine Zweite und 2021 sogar die Dritte. Warum ist das so? Warum steigt die Nachfrage nach 3D-gedruckten Feingussmodellen immer weiter an? Für Thomas Müller sind drei Gründe dafür entscheidend:
Und ich komme trotzdem der Nachfrage an PMMA Modellen nicht hinterher - eigentlich bräuchte ich aktuell noch eine vierte oder fünfte Anlage.
Thomas Müller, FounderExpress Prototyping
Eins, Zwei oder Drei? Am liebsten Vier oder Fünf

Alternative additive Fertigungstechnologien stoßen an Ihre Grenzen
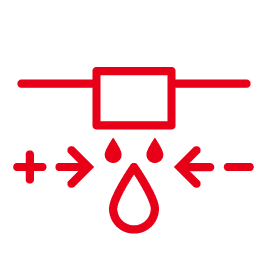
Etablierungsgrad der Binder Jetting Technologie von PMMA mit dessen Vorteilen gegenüber Stereolithographie/Quickcast und Wachsdruckern
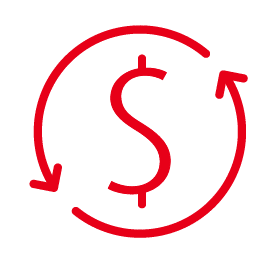
Kostenwirtschaftlichkeit im Großformat und „rapid Time-to-Market“
1. Alternative additive Fertigungstechnologien stoßen an ihre Grenzen
Gemeint sind in diesem Fall, insbesondere Stereolithografie (SLA) oder wachs-basierte, additive Fertigungstechnologien. Beim SLA-Verfahren, werden die Bauteile aus einem flüssigen Kunststoffharz gefertigt. Mittels UV-Licht wird das Harz Schicht für Schicht verbunden. Die Bauteile zeichnen sich durch eine besonders glatte und schöne Oberfläche aus. Eine Alternative zum SLA bieten 3D-Drucker, die Wachs verdruckten. Ein Werkstoff der im Feinguss bestens bekannt ist, da die Modelle beim konventionellen Feingießen in der Regel auch aus Wachs gefertigt werden.
Beide Technologien haben aber Schwierigkeiten, wenn es um die Abformung, sprich die Übertragung des Modells zu einer Keramikform, geht. Die in SLA gedruckten Bauteile neigen dazu, die Schalen beim Ausbrennen der Modelle zu sprengen. Gründe dafür sind meist materialseitig zu identifizieren, da sich die Harze beim Erwärmen ausdehnen. Wachsgedruckte Feingussteile haben dieses Problem nicht, sind aber meist sehr aufwändig in der Handhabung, da unter anderem auch Stützstrukturen gedruckt werden müssen, das Material durchaus teuer ist und die verfügbaren Drucksysteme im Hinblick auf die realisierbaren Bauteilgrößen stark eingeschränkt sind.
„PMMA bietet in dieser Hinsicht den Königsweg. Die Modelle lassen sich sehr schnell und mit der gleichen Kostenwirtschaftlichkeit wie bei den anderen Verfahren fertigen. Bei der Schalenbildung weisen PMMA-Modelle auch bei dünneren Keramikschalen ein hervorragendes Ausbrennverhalten ohne Schalenbrüche vor.“ Erklärt Müller.
Für dieses Ausbrennverhalten ist eine entscheidende Charakteristik des PMMA verantwortlich: sein negativer thermischer Ausdehnungskoeffizient. Das bedeutet, dass das Material schrumpft anstatt sich auszudehnen, wenn es erwärmt wird.
„Wenn SLA voll gedruckt wird, damit meine ich dichte Bauteile ohne Hohlräume, sprengt das jede Schale. PMMA hat hier die perfekte Nische gefunden und erlaubt es uns, sogar Wandstärken von < 1mm problemlos zu realisieren“ führt Müller weiter fort.
Die Oberfläche der PMMA Modelle weist hingegen eine geringfügig höhere Rauigkeit im Vergleich zu den anderen Technologien auf. Diese kann jedoch durch bspw. eine Wachsinfiltration deutlich verbessert werden.
2. Etablierungsgrad der Technologie
Bis 2021 druckten Thomas Müller und sein Team nahezu 100 % technische Bauteile. Motorenkomponenten, Joystickgehäuse für Landwirtschaftsmaschinen, Laufräder und Ersatzteile. Seit 2022 ist seine Produktion zu 70-80 % mit künstlerischen Bauteilen ausgelastet. In technischen Feldern wird die Technologie nach wie vor insbesondere für die Herstellung von Prototypen eingesetzt. Losgrößen bis max. 100 Stück gehören bei Express Prototyping zum Alltagsgeschäft.
„Es ist etwas erstaunlich und ich hätte damit nicht gerechnet. Doch speziell in den letzten Jahren findet PMMA auch immer mehr Anklang in der Kunstszene. Viele Künstler designen mittlerweile komplett in 3D. Aufgrund der möglichen Größe und der einfachen Handhabung erfreut sich das PMMA-Materialset immer größerer Beliebtheit in der kreativen Szene. Mittlerweile hat sich PMMA zu einem neuen Standard im Kunstguss entwickelt, was auch die stets steigende Nachfrage erklärt.“ so Müller.
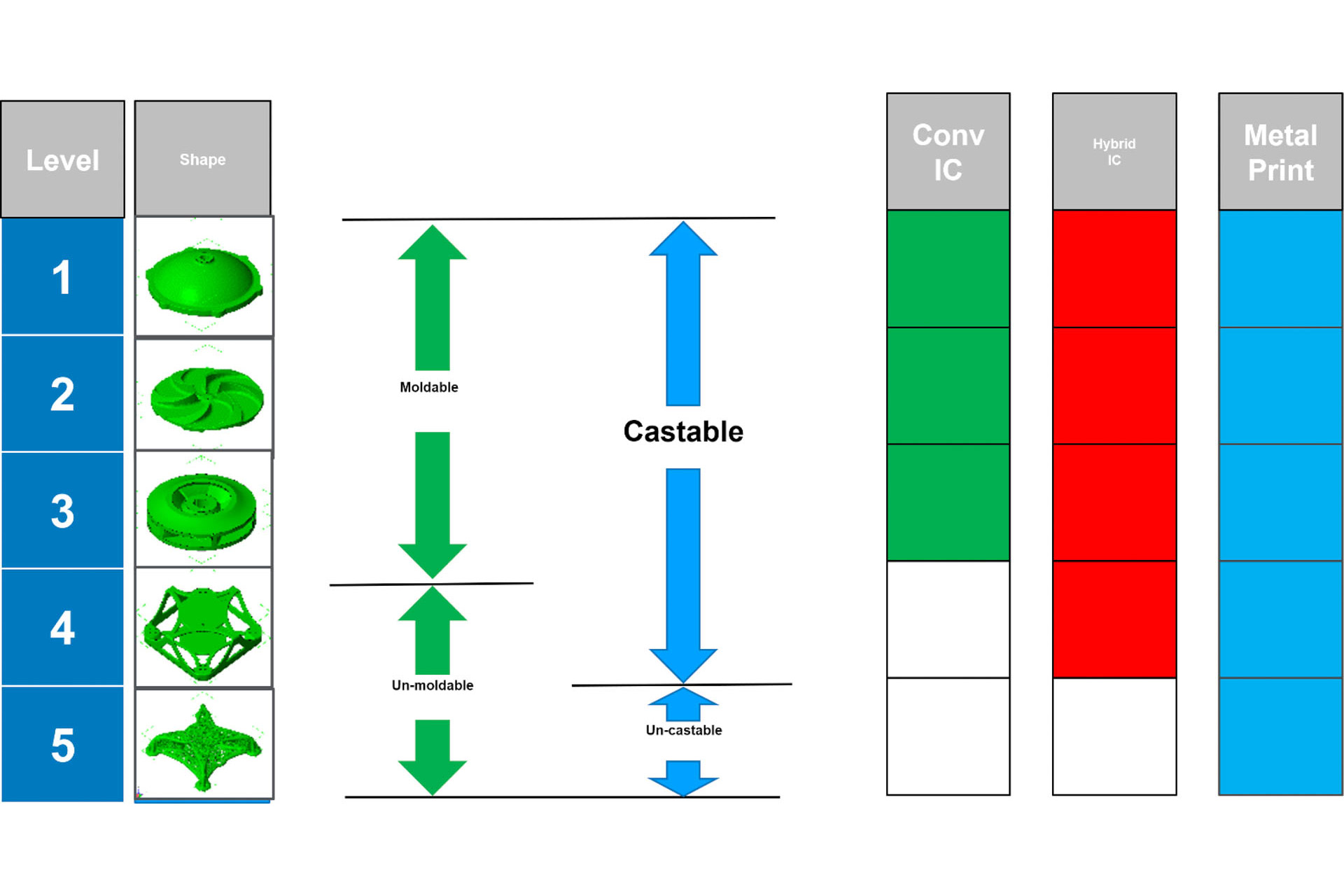
3. Kostenwirtschaftlichkeit im Großformat und „rapid Time-to-Market“
Bis zu 75% an Zeit und Kosten lassen sich einsparen, wenn ein Modell 3D-gedruckt wird, anstatt den Weg über den klassischen Modellbau zu gehen. Der 3D-Druck arbeitet komplett werkzeuglos und CAD-Datenbasiert, so können Designanpassungen direkt digital vorgenommen werden und ein neues Modell gedruckt werden.
„Zur Wirtschaftlichkeit des PMMA 3D-Drucks tragen mehrere Faktoren bei. Dank des einzigartigen Bauvolumens von 1.000 x 600 x 500 mm können neben größeren Einzelbauteilen auch mehrere Produktvariationen gleichzeitig gedruckt werden, was die Kosten pro Stück reduziert. Der Entfall der Werkzeugherstellung via Fräsen o.ä. sorgt sicherlich für die höchste Einsparung. Und auch nicht zu vernachlässigen ist, dass unverdrucktes Material recycelt und wiederverwendet werden kann. So lässt sich auch der Pulververbrauch und laufenden Kosten optimieren.“ resümiert Müller.
Auch bei Betrachtung der nach dem 3D-Druck gelagerten Prozessschritte, hat PMMA das Potenzial, Prozessschritte zu verschlanken, zu reduzieren und Kosten einzusparen. Beispielsweise beim oben bereits erwähnten Schalenaufbau. Dank der Ausbrenneigenschaften des PMMAs können teilweise weniger Keramikschichten um das Modell gelegt werden, sodass diese deutlich schneller trocknen und für den Abguss vorbereitet werden.
Ist das die Zukunft des Feingießens?
Bei all den obigen Informationen und Argumenten stellt sich die Frage, ob sich der PMMA-3D-Druck in anderen Industriezweigen, abseits der Kunstszene, zu einem Standard für den Feinguss entwickeln könnte. Geht es um Massen- und Serienfertigung, wird kein additives Verfahren in nächster Zukunft die etablierten Verfahren und Technologien ablösen. Bis es soweit ist, müssen Materialien und Systeme noch günstiger und Automationslösungen weiterentwickelt werden.
Es sei denn Kunden entwickeln künftig mehr und mehr Bauteile, die ausschließlich über 3D Druck gefertigt werden können.
Thomas Müller, FounderExpress Prototyping
Betrachtet man nur den 3D-Druck, zeichnet sich ein etwas anderes Bild. „Jedes additive Verfahren hat seine Vor- und Nachteile. Entscheidend sind die Kunden und deren Anforderungen. Im Kunstbereich erfüllt PMMA die Anforderungen der Künstler ideal. Wenn bei technischen Bauteilen eine gute Oberfläche wichtiger ist, eignet sich, je nach Bauteil, ggf. der Wachsdruck besser.“ so Müller.
Etwas anders sieht er es für den 3D-Druck im Allgemeinen: „Der 3D-Druck wird auch in Zukunft eine große Rolle spielen, so viel ist sicher. Schauen wir sehr weit voraus, kann meiner Meinung nach dem direkten Metall 3D-Druck (DMLS – Direct Metal Laser Sintering), sicher ein dominanter Player werden, wenn es um die Herstellung von Metallteilen geht. Bis es soweit ist, müssen aber Materialien günstiger und die Anlagen produktiver werden. Stand heute, sind mir keine Gießereien bekannt, in DMLS-Anlagen investiert“ erklärt der Maschinenbauer. „Bis dahin ist PMMA weiter eine sinnvolle Ergänzung, um schnell, wirtschaftlich und mit hoher Präzision Feingussteile herzustellen.“ schließt Müller ab.
Weiterentwicklungen des PMMA-Prozesses sorgen auch in Zukunft dafür, dass der 3D-Druck von Feingussmodellen weiter Fuß gewinnt. So ist es bspw. schon heute möglich mittels 3D-Druck von keramischen Kernen, die mit in PMMA gedruckten Modellen kombiniert werden können, noch komplexere Strukturen gießbar zu machen. Auch hinsichtlich der für Thomas Müller erforderlichen Produktivitätssteigerungen bieten sich Lösungsansätze. So ist ein grundlegender Vorteil der Binder Jetting Technologie, dass sie sich mehr oder weniger leicht skalieren lässt. So ist es auch denkbar, dass es in Zukunft, neben dem aktuell größten 3D-Druckers für PMMA, der VX1000, in Zukunft auch noch größere Systeme, wie bspw. eine VX2000, mit einem Bauvolumen von 2.000 x 1.000 x 1.000 mm geben wird. Ein erster Prototyp dafür befindet sich bereits im Feld. Bis dahin, werden die Jobboxen bei Express Prototyping weiter im Akkord getauscht und die Etablierung eines neuen Standards weiter beobachtet und aktiv vorangetrieben.
Weitere Case Studys
Mit 3D-Druck zum Optimierten Elektromotor
Aiona Cast hat ein Patent angemeldet mit dem sich Elektromotoren deutlich optimieren lassen. Einen Prototyp fertigte das Unternehmen mit 3D-Druck an.
Die schnellste Gießerei Skandinaviens
Mit einer neuen VX2000, einem 3D-Sanddrucker für Metallguss stellt Hetitec fertige Gussteile in wenigen Tagen her.
Printed Castings für den Feinguss
Ob Luft- und Raumfahrt, Automobilbau oder Design - die preisgekrönte, amerikanische Feingießerei Aristo Cast setzt beim Feinguss auf 3D-gedruckte Modelle. Erfahren Sie hier warum.
Printed Casting Gehäuse für E-Motorrad
Durch den Einsatz innovativer Technologien wie dem 3D-Druck könnte der Prototyp schon bald in Serie gehen.
3D-Druck für Sandguss in Portugal
CINFU ist ein Ausbildungs- und Innovationszentrum für die Gießereiindustrie mit Sitz in Portugal. Mit einem VX1000 3D-Drucker im Haus gewinnt CINFU erhebliche Vorteile bei der Anpassung an die Gießereiindustrie.
Lanulfi Models optimiert Formenbau mit VX2000
Die Integration der voxeljet VX2000 hat Lanulfis Ansatz im Modell- und Formenbau neu definiert. Sie bietet erhebliche Reduzierungen der Durchlaufzeiten und verbessert die Gestaltungsmöglichkeiten.
Boro Foundry – Superheater Header
Aus der Kombination Sand-3D-Druck konnte die britische Gießerei Boro Foundry ein makelloses Ersatzteil für eine Dampflok herstellen.
Mit 3D-Druck zum Optimierten Elektromotor
Aiona Cast hat ein Patent angemeldet mit dem sich Elektromotoren deutlich optimieren lassen. Einen Prototyp fertigte das Unternehmen mit 3D-Druck an.
Die schnellste Gießerei Skandinaviens
Mit einer neuen VX2000, einem 3D-Sanddrucker für Metallguss stellt Hetitec fertige Gussteile in wenigen Tagen her.
Printed Castings für den Feinguss
Ob Luft- und Raumfahrt, Automobilbau oder Design - die preisgekrönte, amerikanische Feingießerei Aristo Cast setzt beim Feinguss auf 3D-gedruckte Modelle. Erfahren Sie hier warum.
Printed Casting Gehäuse für E-Motorrad
Durch den Einsatz innovativer Technologien wie dem 3D-Druck könnte der Prototyp schon bald in Serie gehen.
3D-Druck für Sandguss in Portugal
CINFU ist ein Ausbildungs- und Innovationszentrum für die Gießereiindustrie mit Sitz in Portugal. Mit einem VX1000 3D-Drucker im Haus gewinnt CINFU erhebliche Vorteile bei der Anpassung an die Gießereiindustrie.
Lanulfi Models optimiert Formenbau mit VX2000
Die Integration der voxeljet VX2000 hat Lanulfis Ansatz im Modell- und Formenbau neu definiert. Sie bietet erhebliche Reduzierungen der Durchlaufzeiten und verbessert die Gestaltungsmöglichkeiten.
Boro Foundry – Superheater Header
Aus der Kombination Sand-3D-Druck konnte die britische Gießerei Boro Foundry ein makelloses Ersatzteil für eine Dampflok herstellen.
Mit 3D-Druck zum Optimierten Elektromotor
Aiona Cast hat ein Patent angemeldet mit dem sich Elektromotoren deutlich optimieren lassen. Einen Prototyp fertigte das Unternehmen mit 3D-Druck an.
Kontakt
Möchten Sie mehr erfahren? Dann fragen Sie uns. Wir helfen Ihnen gerne weiter.
Industrielle 3D-Drucksysteme
Unser Portfolio an industriellen 3D-Druckern reicht vom kompakten System für die Forschung bis zur additiven Serienfertigung.