- Home
- Case Studies
- Konsumgüter
- HP Multi Jet Fusion und voxeljet High Speed Sintering im Vergleich
HP Multi Jet Fusion und voxeljet High Speed Sintering im Vergleich
Im Rahmen der additiven Fertigungstechnologie „Powder Bed Fusion“ haben sich mittlerweile neben dem Selektiven Laserschmelzen (SLS) zwei weitere, tintenstrahlbasierte 3D-Druckverfahren fest etabliert. Zum einen die Multi Jet Fusion Technologie von HP und zum anderen die High Speed Sintering Technologie (HSS) von voxeljet. Doch wo genau liegen die Unterscheide der beiden Verfahren? Wo lassen sich die Technologien wirtschaftlich einsetzen? Und was macht HSS zu einer attraktiven Alternative zum Multi Jet Fusion?
Beide Binder Jetting Technologien zeigen einzigartige Vorteile wie beispielsweise im Hinblick auf Druckgeschwindigkeiten, Bauraumvolumen und damit einhergehend den Teilekosten auf. Ein gravierender Unterschied liegt aber in der Anpassbarkeit der Prozesstechnologien und der verarbeitbaren Materialvielfalt. Aber klar ist, mit beiden Verfahren lassen sich eine Vielzahl von Anwendungen realisieren – schnell und wirtschaftlich.
Die beiden 3D-Druck Verfahren in der Anwendung
Hewlett-Packard (HP) ist ohne jeden Zweifel einer der führenden Druckerhersteller weltweit. Mit einem breiten Erfahrungsschatz für Tintenstrahltechnik ist es wenig verwunderlich, dass sich das Unternehmen 2017 dazu entschloss mit seiner Multi Jet Fusion (MJF) Technologie in das 3D-Druck-Geschäft einzusteigen. Heute finden 3D gedruckte Multi Jet Fusion Teile (gedruckt in PA 12) dank ihrer guten Hitzebeständigkeit und mechanischen Belastbarkeit in einer Vielzahl von Bereichen Anwendung. Darunter der Automobilbau, Maschinenbau und die Sport- und Freizeitindustrie.
Beim Multi Jet Fusion Verfahren wird mittels eines Druckkopfes eine strahlungsabsorbierende Tinte in ein weißes Pulverbett, bspw. aus Polyamid 12 (PA12) eingetragen. Nicht zu bedruckende Flächen werden dagegen mit einem zweiten Druckfluid, einem Detailing-Agent, abgekühlt. Dabei arbeitet der Drucker schichtbasiert nach einem digitalen CAD-Datensatz. Nach dem Bedrucken des Pulverbettes wird in dieses nach jeder Schicht mit einer Infrarot-Lampe Energie eingetragen. Die schwarz eingefärbten Teilbereiche des Pulverbettes absorbieren mehr Energie und verschmelzen, während das weiße Pulver, dank des Detailing-Agents, unverschmolzen bleibt. Diese Prozessreihenfolge wiederholt sich bis das gesamte Bauvolumen der Jobbox gefüllt und die benötigen Bauteile innerhalb des Pulverbettes fertig gedruckt sind.
Die Polymer High Speed Sintering (HSS) Technologie von voxeljet unterscheidet sich in der Verfahrensweise nur bedingt von dem Multi Jet Fusion Verfahren. Auch beim HSS wird über einen Druckkopf ein Energie-Absorber ein weißes Pulverbett eingetragen, in welches ebenfalls IR-Energie eingetragen wird.
Genau wie beim MJF-Verfahren verschmelzen die gefärbten Teilbereiche des Pulverbettes, währenddessen unbedrucktes Pulver lose bleibt. Ein zweites kühlendes Fluid ist beim HSS nicht notwendig, da mittels zweier verschiedener IR-Strahler unterschiedlicher Wellenlänge mit Absorber bedrucktes und unbedrucktes Pulvermaterial unabhängig voneinander in ihrer Temperatur geregelt werden können. Das unberdruckte Pulver kann genau wie bei MJF recycled, aufbereitet und erneut in den Prozesskreislauf eingespeist werden.
Was die Bauteilqualität und auch die Anwendungsmöglichkeiten angeht, steht die HSS Technologie dem Multi Jet Fusion in nichts hinterher. Jedoch ist die voxeljet VX1000 HSS durch ihre Größe industrietauglicher und günstiger in den Verbrauchskosten als die aktuellen Drucker von HP, wodurch sich die Kosten pro Teil deutlich verringern. Darüber hinaus erlaubt voxeljet seinen Kunden, uneingeschränkt ihre eigenen Materialien zu verwenden, und gewährt Endanwendern vollen Zugang zu den Druckparametern, um die Produktion für das jeweilige Material und die jeweilige Anwendung zu optimieren. Ein Vorteil, der insbesondere bei großvolumigen Bauteilen oder Losgrößen für die Serienproduktion zum Tragen kommt. So können auch HSS gedruckte Bauteile in verschiedensten Industriezweigen wie der Architektur, dem Automobilbau und Sportindustrie eingesetzt werden.
3D-Drucksysteme Multi Jet Fusion und High Speed Sintering im Vergleich
HSS
MJF
Anwendungsbereiche
Materialentwicklung & -forschung
Prototypenbau
Produktionsanwendungen
Dienstleistungszentren
verarbeitendes Gewerbe
Spritzgussunternehmen
Prototypenbau
Dienstleistungszentren
Produktionsanwendungen
Bauraum
VX200 HSS: 290 x 140 x 180 mm
VX1000 HSS: 1.000 x 540 x 400* mm
MJF 540/580: 322 x 190 x 248 mm
MJF 4200: 380 x 285 x 380 mm
MJF 5200: 380 x 294 x 380 mm
Geschwindigkeit
VX200 HSS: 580 cm³/h
VX1000 HSS: 6.500 cm³/h
MJF 540/580: 1.817 cm³/h
MJF 4200: 4115 cm³/h
MJF 5200: 5058 cm³/h
Auflösung
360 dpi
1200 dpi
Materialien
PA12
TPU
PP
PEBA
EVA
PA12
PA11
TPA
TPU
Genauigkeit
±0.3% (with a lower limit on ± 0.3 mm)
±0.3% (with a lower limit on ± 0.3 mm)
Minimale Schichtstärke
80 µm
80 µm
Festigkeiten (PA12)
VX200 HSS
Methode: ISO 527 – 2:93 – 1A
E-Modul (XY): 1716 MPa
E-Modul (Z): 1725 MPa
Zugfestigkeit (XY): 52 MPa
Zugfestigkeit (Z): 46 MPa
Bruchdehnung (XY): 10 %
Bruchdehnung (Z): 5 %
MJF 4200
Methode: ASTM D3418
E-Modul (XY): 1700 MPa
E-Modul (Z): 1800 MPa
Zugfestigkeit (XY): 48 MPa
Zugfestigkeit (Z): 48 MPa
Bruchdehnung (XY): 20 %
Bruchdehnung (Z): 15 %
Abkühlzeiten
Ohne fast cooling: 14h***
Ohne fast cooling: 48 h*
Mit fast cooling: k. A
Post processing
Kompatibel mit den meisten verfügbaren Nachbearbeitungslösungen
Automatisches Mischen, Sieben und Befüllen, halb manuelles Entladen, Fast Cooling, externer Vorratsbehälter
* abhängig von Material und Korngröße
** voxeljet erlaubt dem Kunden, jedes Material auf eigenes Risiko zu verwenden und kann eine Beratung zur Materialauswahl anbieten.
*** abhängig von der Bauhöhe
Wo liegen die Unterschiede von MJF und HSS?
Das Multi Jet Fusion Verfahren arbeitet mit zwei Arten von Flüssigkeiten zum Drucken der Bauteile. Beim Energieabsorber, auch Fusion Agent genannt, handelt es sich um eine wasserbasierte, strahlungsabsorbierende Tinte, die die entsprechenden Bereiche des Pulverbettes schwarz einfärbt. Um eine präzise Kantenschärfe zu erzielen, wird noch eine zweite Flüssigkeit, der sogenannte Detailing Agent, in die äußeren Randbereiche des zu druckenden Bauteiles eingetragen, um die Kanten der Bauteile vor dem Sintervorgang zu kühlen und so eine erhöhte Präzision zu gewährleisten. Zudem zeichnet sich die Bubble-Jet-Druckkopftechnologie durch eine hohe, theoretische Auflösung von 1200 dpi aus.
Mit einem im Vergleich zur HSS Technologie höheren Bauvolumen und schnelleren Schichtzeiten und einer „Plug and Play“-Lösung, eignet sich MJF gut für den Einsatz im Prototypenbau, Dienstleistungszentren und Produktionsanwendungen. Bereits verfügbare Materialien für das Multi Jet Fusion sind unter anderem verschiedene PA12 varianten, sowie TPA, TPU, PP und PA11.
Im Gegensatz zum Multi Jet Fusion arbeitet die HSS-Technologie mit einem Piezo-Druckkopf und lediglich einem Energieabsorber. Beim Energieabsorber handelt es sich um eine ölbasierte Tinte, mit der das Pulverbett eingefärbt wird. Durch besonders präzise Lichtwellensteuerung und Wellenlängen-Definition kann die IR Energie gezielt in das Pulverbett eingetragen werden, und zwar nur dort wo Bauteile entstehen sollen. Diese präzise Steuerung resultiert in äußerst scharfen Kantendetails.
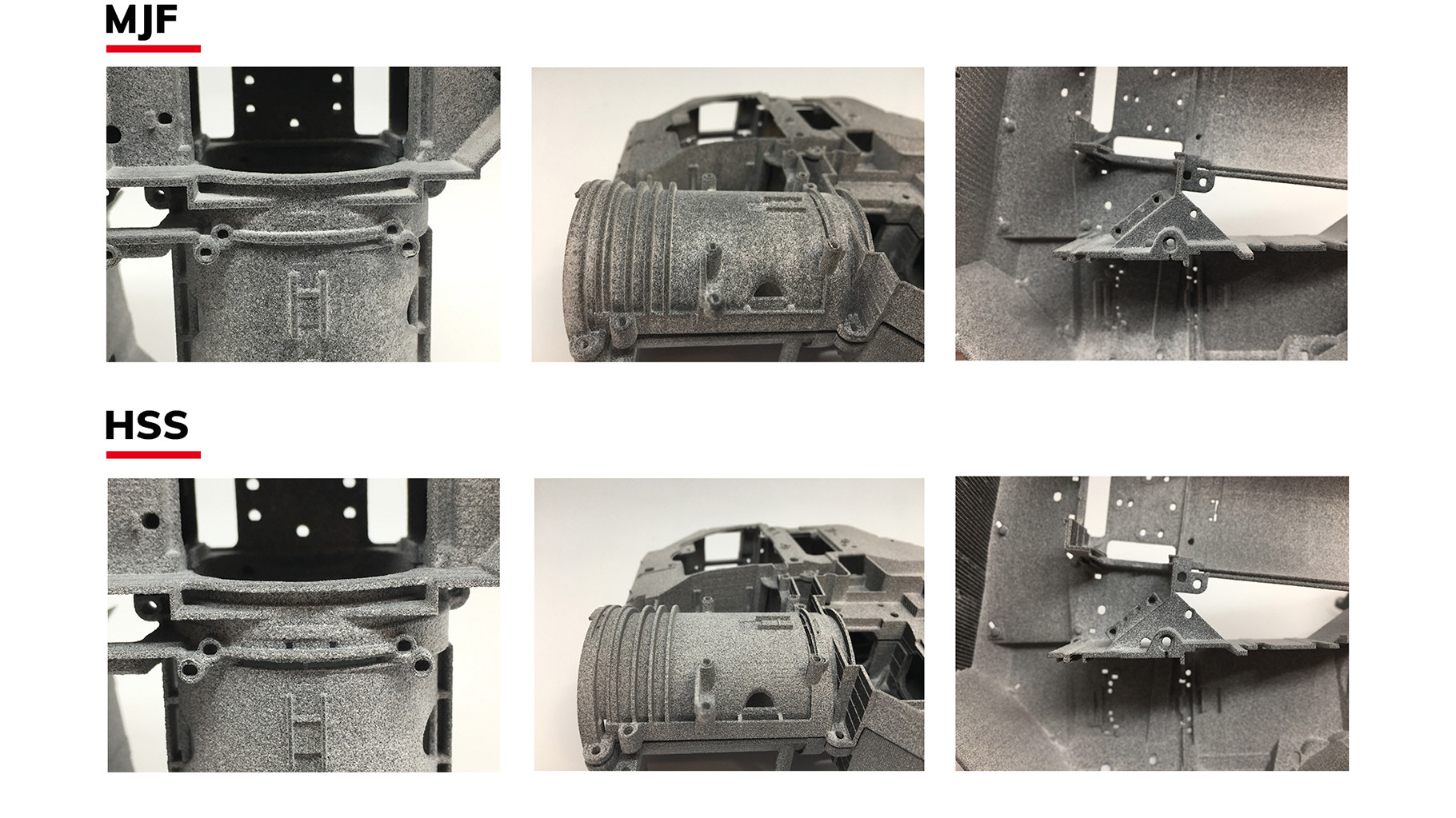
Vergleich Kantendetails MJF & HSS
Der Druckkopf arbeitet dabei mit einer Lösung von 360 dpi. Da bei Powder Bed Fusion Technologie jedoch die Korngröße des zu verdruckenden Pulvers die entscheidende Variable für die Auflösung ist, ist eine höhere Druckkopfauflösung auch nicht notwendig, sondern vielmehr das Zusammenspiel mit dem Thermomanagement für die Detailtreue entscheidend. Der industrielle Inkjet-Druckkopf ist optimal auf die Tinte abgestimmt, was in erhöhten Druckkopf-Haltbarkeiten resultiert. Neben ölbasierten können die Inkjet-Druckköpfe auch wasser- und lösemittelbasierte Fluide verarbeiten.
Webinar: HSS 3D-Druck
In diesem Workshop werden wir unsere HSS-Technologie im Detail vorstellen: Von der Open-Source-Konzeption bis hin zu Skalierungs- und Produktionsmöglichkeiten.
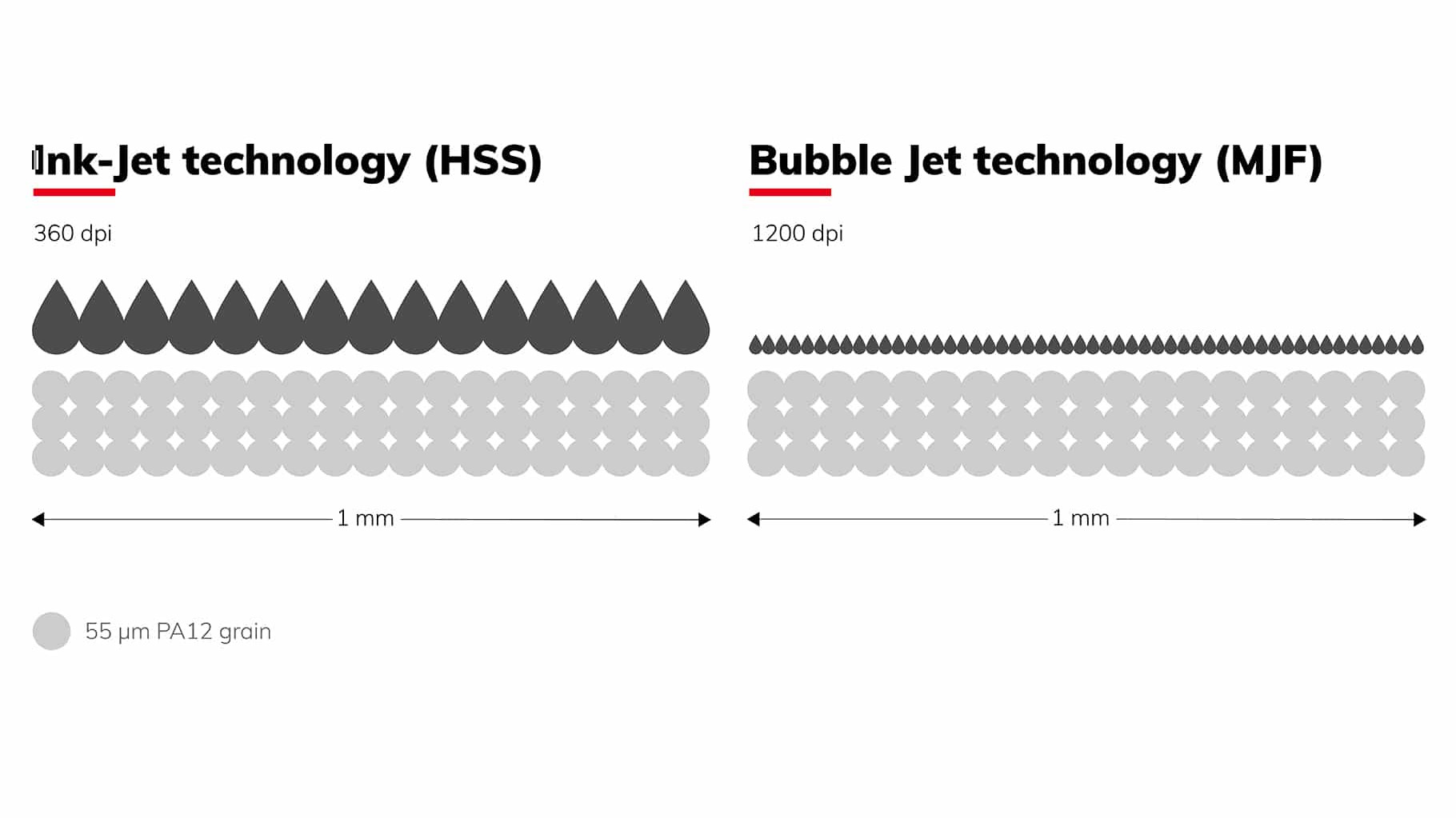
Vergleich Auflösung MJF & HSS Technologie
Ein weiterer Unterschied zum Multi Jet Fusion ist der Open-Source Ansatz der HSS Technologie. Nutzern steht mit HSS-3D-Drucksystemen ein offener 3D-Drucker zur Verfügung, in dem sämtliche Prozessparameter frei zugänglich und individuell an eigene Materialien angepasst werden können. Somit eignet sich die HSS-Technologie ideal zur individuellen Entwicklung von neuen 3D-Druckpolymeren für optimale Teileeigenschaften. Die entwickelten Prozessparameter lassen sich zum Einsatz auf einem größeren voxeljet 3D-Drucksystemes wie bspw. der VX1000 HSS skalieren, um auch größere Produktionsvolumina und Stückzahlen wirtschaftlich zu drucken. Die Vorteile des Open-Source Ansatzes, sowie der Einsatz eines einzelnen Absorbers spiegeln sich auch in den laufenden Kosten wider. Während die Systeme bei Betrachtung der Anschaffungskosten in einer ähnlichen Preisklasse liegen, so können HSS Anlagen auch mit kundeneigenen Pulvern betrieben werden, während der Verbrauch eines einzelnen Absorbers die laufenden Kosten weiter reduziert.
Weitere Unterschiede gibt es bei der Materialauswahl. So können mittels HSS, durch die Möglichkeit der flexiblen Anpassung des Systems an das gewünschte Material, sowie dem Verwenden von nur einer ölbasierten Tinte, Polymere wie PA12, PA6, PP, PEBA, EVA und TPU verarbeitet werden. Bislang konnten Pulverkorngrößen von 30 µm bis 1 mm bereits erfolgreich verarbeitet werden.
Sie möchten mehr über die HSS Technologie erfahren? Dann schauen Sie sich doch unsere Whitepaper an:
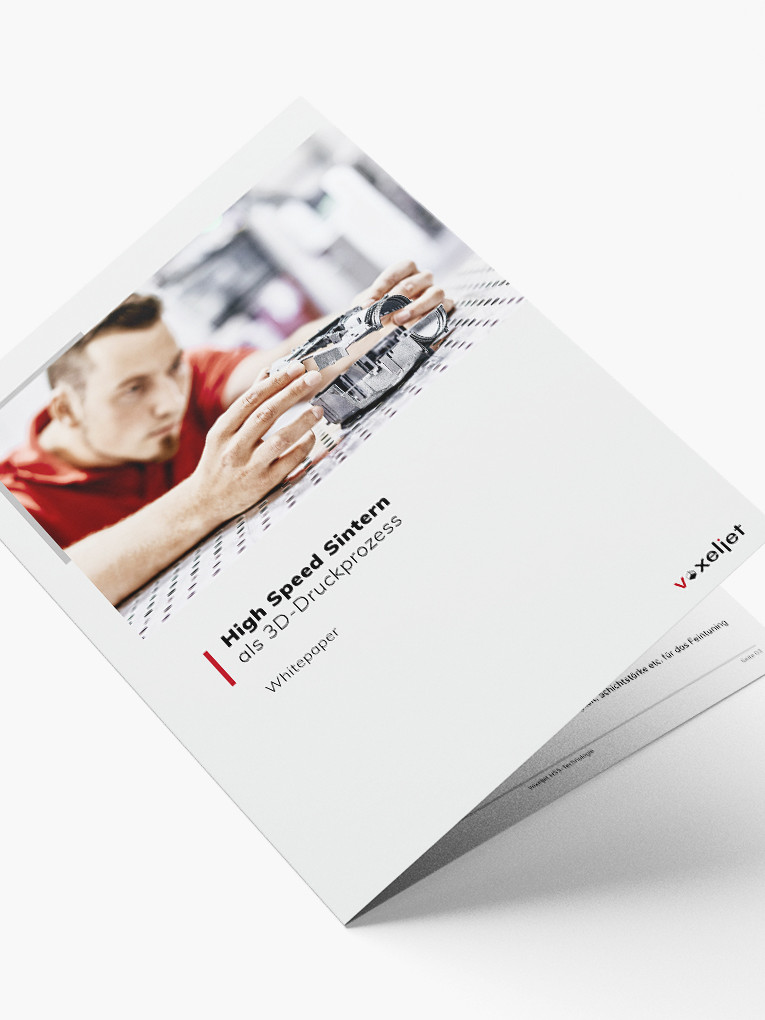
WhitepaperHigh Speed Sintering (HSS)
Im Gegensatz zu herkömmlichen Verfahren erfolgt das Polymer Sintering nicht über komplexe Lasertechnologie, sondern pixelgenau über wärmereaktive Binder.
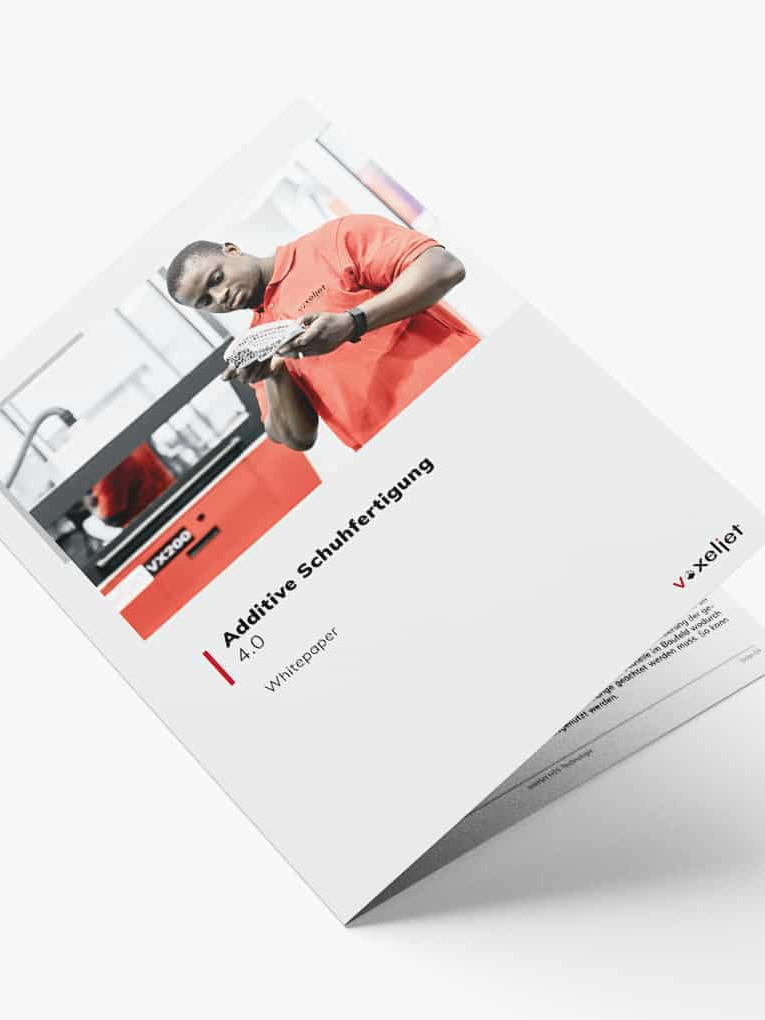
WhitepaperAdditive Schuhfertigung 4.0
Polymer High Speed Sintering ermöglicht maßgefertigte Schuhe, die den Verbrauchern sogar leistungs- und komfort-steigernde Funktionen bieten könnten.
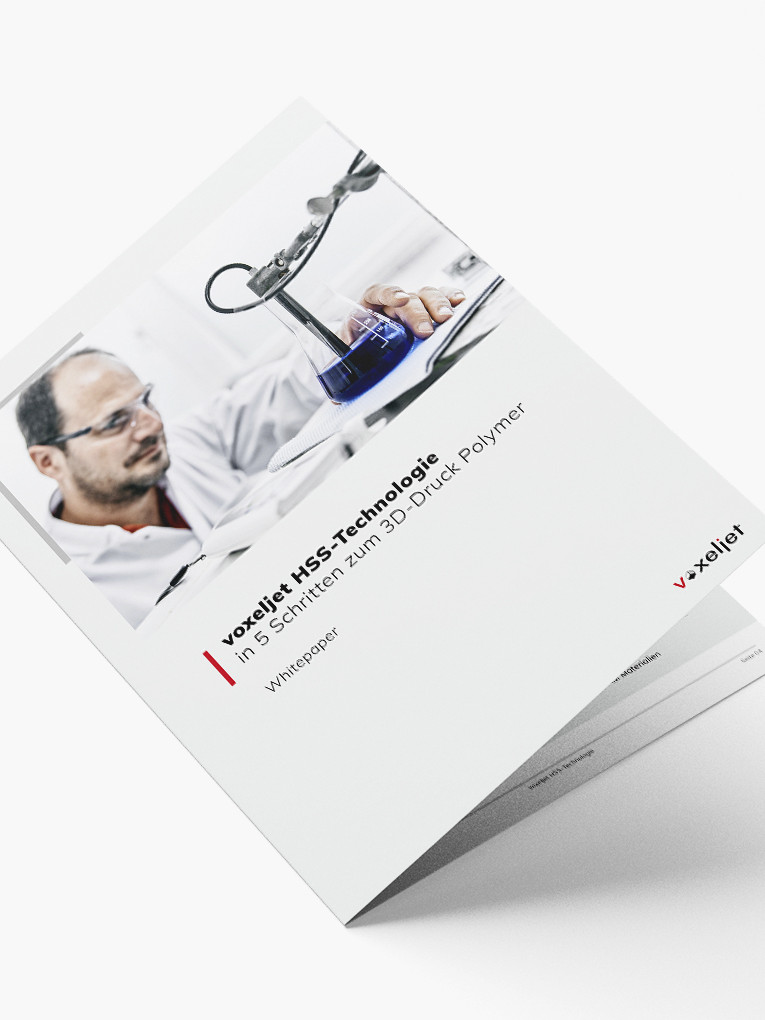
Whitepaper3D-Druck Polymer Qualifizierung
In diesem Whitepaper zeigen wir Ihnen den gesamten Workflow und die Besonderheiten auf die es bei der Materialqualifizierung zu achten gilt.
Weitere Case Studies
Was ist der Unterschied zwischen HSS-, MJF- und SLS-Polymer-3D-Druck? Lernen Sie die drei wichtigsten AM-Technologien für Polymere in diesem umfassenden Vergleich kennen.
HSS Material Network – Proof of Concept HDPE
Gemeinsam mit dem Fraunhofer IPA haben wir im Rahmen des HSS Materil Netoworks Polymer HDPE für die additive Fertigung qualifiziert.
Polymer Sintering im Sondermaschinenbau
Mit High Speed Polymer Sintering lassen sich Prototypen wesentlich schneller und wirtschaftlicher realisieren.
Mit 3D-Druck zum perfekten Sneaker
Wie sich mittels Polymer High Speed Sintering (HSS) der perfekte 3D gedruckte Schuh entwickeln lässt.
3D-gedruckte Joysticks für Traktoren und Maschinen
Für die Lindner Traktorenwerke ist der 3D-Druck bereits heute eine Alternative zum Spritzguss. Unter anderem für individualisierte Joysticks und Bedienelemente Ihrer Traktoren.
URWAHN – 3D-Druck im Fahrradbau
Bei der Produktion seiner E-Bikes setzt URWAHN auf Reshoring und Lean Management und erreicht diese Ziele durch additive Fertigung. Erfahren Sie, welche Rolle die Voxeljet-Technologie dabei spielt.
HSS Material Network – Proof of Concept TPU Launhardt
Das HSS Material Network hat ein neues Proof of Concept veröffentlich. Das TPU des Herstellers Launhardt gehört zu den weichsten am Markt.
Was ist der Unterschied zwischen HSS-, MJF- und SLS-Polymer-3D-Druck? Lernen Sie die drei wichtigsten AM-Technologien für Polymere in diesem umfassenden Vergleich kennen.
HSS Material Network – Proof of Concept HDPE
Gemeinsam mit dem Fraunhofer IPA haben wir im Rahmen des HSS Materil Netoworks Polymer HDPE für die additive Fertigung qualifiziert.
Polymer Sintering im Sondermaschinenbau
Mit High Speed Polymer Sintering lassen sich Prototypen wesentlich schneller und wirtschaftlicher realisieren.
Mit 3D-Druck zum perfekten Sneaker
Wie sich mittels Polymer High Speed Sintering (HSS) der perfekte 3D gedruckte Schuh entwickeln lässt.
3D-gedruckte Joysticks für Traktoren und Maschinen
Für die Lindner Traktorenwerke ist der 3D-Druck bereits heute eine Alternative zum Spritzguss. Unter anderem für individualisierte Joysticks und Bedienelemente Ihrer Traktoren.
URWAHN – 3D-Druck im Fahrradbau
Bei der Produktion seiner E-Bikes setzt URWAHN auf Reshoring und Lean Management und erreicht diese Ziele durch additive Fertigung. Erfahren Sie, welche Rolle die Voxeljet-Technologie dabei spielt.
HSS Material Network – Proof of Concept TPU Launhardt
Das HSS Material Network hat ein neues Proof of Concept veröffentlich. Das TPU des Herstellers Launhardt gehört zu den weichsten am Markt.
Was ist der Unterschied zwischen HSS-, MJF- und SLS-Polymer-3D-Druck? Lernen Sie die drei wichtigsten AM-Technologien für Polymere in diesem umfassenden Vergleich kennen.
Kontakt
Möchten Sie mehr erfahren? Dann fragen Sie uns. Wir helfen Ihnen gerne weiter.
3D-Drucklösungen
Sie möchten mehr über uns und den 3D-Druck erfahren? Hier geht’s zum gesamten Lösungsportfolio von voxeljet.